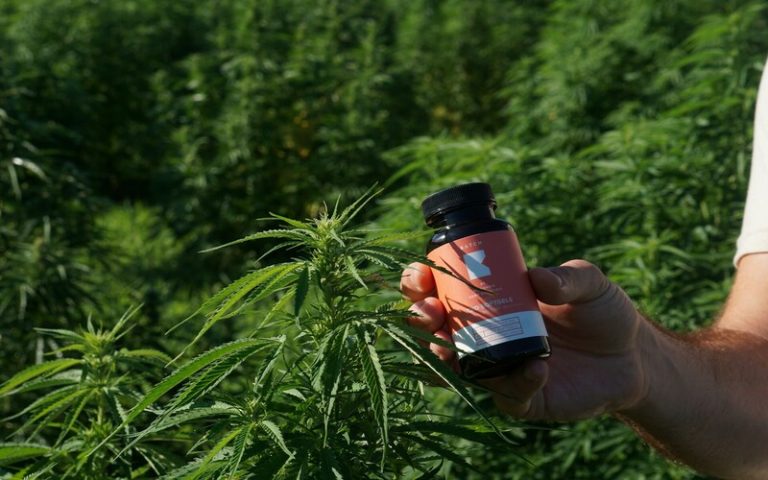
[ad_1]
Traditionally, product design and prototyping processes in the cannabis industry have been time-consuming and expensive. However, with the introduction of 3D printing technology, these processes have become much more streamlined and efficient.
3D printing allows for a level of tailoring that was previously unattainable in manufacturing methods. With the ability to produce elaborate designs and distinctive forms, manufacturers can now cater to their customer’s specific needs and preferences. This is especially beneficial in the cannabis industry, where packaging is crucial in product differentiation and brand identity.
This article will explore in further detail the role of 3D printing in cannabis manufacturing and how it can change how products are designed, packaged, and marketed.
Why 3D Printing Is Essential for Cannabis Package Manufacturing
The modernization of cannabis policies across various regions has sparked a wave of scientific and technological innovations in the industry. With more countries legalizing cannabis for medical and recreational use, there has been a surge in research and development aimed at unlocking the plant’s full potential. From genetic engineering to precision cultivation techniques, the scientific understanding of cannabis has deepened, leading to the development of new strains with tailored cannabinoid profiles and enhanced therapeutic properties.
However, as cannabis legalization expands to new areas, so does the demand for cannabis products, necessitating complex and customizable packaging and designs that typical manufacturing methods may not be able to fulfill. 3D printing, with its ability to produce unique designs quickly, can bridge this gap by creating streamlined, cost-effective production processes and meeting the demands of a growing market.
Additionally, 3D printing can reduce waste and improve sustainability. With traditional manufacturing methods, excess materials are often discarded after production. However, with 3D printing, manufacturers can print only what is needed, reducing material waste and carbon footprint.
Streamlining Product Design and Prototyping Processes
Prototyping for cannabis product packaging can be laborious, requiring multiple iterations before a final product is achieved. This prolongs the development phase and adds to manufacturing costs. With 3D printing, manufacturers and designers can make real-time design and packaging adjustments that ultimately cut down on both costs and time.
Furthermore, the introduction of multi-material 3D printing lets you deposit multiple materials simultaneously, opening up possibilities for elaborated designs and functional prototypes with exceptional accuracy and detail. This technology empowers designers to explore innovative shapes, textures, and structures, pushing the boundaries of creativity in cannabis product design. From vaporizer designs to intricately patterned packaging, the potential applications of 3D printing in cannabis manufacturing are vast and diverse.
Enhancing Process Improvement and Competitiveness
In an increasingly competitive market, efficiency and agility are paramount for success. Herein lies the relevance of 3D printing as a revolutionary tool to enhance and improve the business process. By simplifying the product development lifecycle, from concept ideation to prototyping and production, 3D printing accelerates time-to-market, removes tedious and manual processes, and reduces development costs.
Moreover, customizable packaging solutions, made possible through 3D printing, offer a distinct technological competitive advantage for cannabis companies. Compared to regular packaging materials, which are often limited in design flexibility and customization options, 3D-printed packaging allows for tailored solutions that meet both brands’ and consumers’ unique needs and preferences.
Recycled materials, a popular choice for environmentally conscious consumers, can be seamlessly integrated into 3D-printed packaging, aligning with sustainability initiatives and enhancing brand reputation. Additionally, using biodegradable and compostable materials further underscores the industry’s commitment to environmental stewardship.
Product freshness and safety are also key considerations in the cannabis industry. With 3D printing, manufacturers can create unique packaging solutions with built-in tamper-evident features to ensure product integrity, child-proofing designs to comply with regulations, and even incorporate technologies such as RFID tags for tracking and authentication purposes.
The Transformative Potential of 3D Printing in Cannabis Manufacturing
The adaptation of 3D printing technology has already significantly impacted the cannabis industry, and its potential for further transformation is immense. Let’s explore some possible future applications of 3D printing in cannabis manufacturing:
- Customized medications: Cannabis-based medicines can be customized with specific dosages and cannabinoid ratios for individual patients.
- Novel delivery systems: Traditional methods of consuming cannabis, such as smoking and vaping, may not be suitable for all consumers. 3D printing can create innovative delivery systems that cater to diverse preferences, such as edible capsules or transdermal patches.
- On-demand production: The ability to produce products on-demand with 3D printing eliminates the need for large-scale inventory storage and reduces waste, making it a more sustainable and cost-effective production method.
- Collaborative design and production: 3D printing allows real-time collaboration between designers, manufacturers, and cannabis companies. This can result in the formation of distinctive products catering to specific market segments and trends.
- Safe and sustainable packaging solutions: From child-resistant packaging to tamper-evident seals, 3D printing offers a range of options for creating secure and sustainable packaging solutions that comply with industry regulations.
3D printing is a game-changer in cannabis manufacturing, offering endless possibilities for product design, process improvement, and sustainable production. As research and development continue to realize the maximum capacity of this technology, we can expect to see even more groundbreaking applications in the future.
[ad_2]
Source link